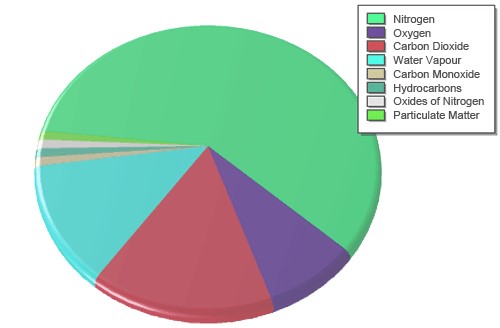
With all engines, what goes in must come out. If you put in 1kg of fuel and 25kg of air, at the other end the result will be 26kg of exhaust emissions. All the atoms that went in will have come out too, but not necessarily as part of the same compounds they were in before.
The emissions form internal combustion engines burning hydrocarbons can be broken down into four categories:
1. Residues of the intake air: Primary oxygen and nitrogen. As far as we know, these are completely harmless.
2. Products of components in the intake air: The most significant under this heading are the “oxides of nitrogen”, which have varying degrees of toxicity.
3. Products of complete combustion: These comprise carbon dioxide and water vapor, which although non-toxic, are both considered to be greenhouse gases and are therefore implicated in climate change.
4. Products of incomplete combustion: These include carbon monoxide, hydrocarbons, and particulate matter, all of which are toxic.
The toxic substance contained in exhaust gas as it leaves the engine are known as ‘primary pollutants’, but once they have left the engine some of these may react with each other or with other compound present in the atmosphere to create what are known as ‘ secondary pollutants’. Examples of secondary pollutants include ozone, acid rain and photochemical smog.
- There was a proposal from a previous SIMRAC project to implement a target value of 0.350mg/m³ total carbon (TC) and to further reduce the target value over the years.
- Internationally, DPM is regulated via two mechanisms i.e. Occupations Health and Safety Standards (OELs) and Tailpipe Emission Standards.
- Section 21 of the Mine Health and Safety Act ( Act 29 of 1996) requires the manufacturers and suppliers to ensure that articles are safe and do not pause a risk to health and safety of employees who may use such article.
Proposed Regulatory Framework for DPM.
(Form the Department of Mineral Resources, www.drm.gov.za)
- Higher quality diesel fuel is used
- Latest generation diesel engines are used
- Maintenance staff is adequately trained and available for employment to work on these, units
- Exhaust fume purification systems are used extensively.
The advised step in approach is detailed as follow:
- A DPM exposure control value of 350 μg/m³ (TC) up to December 2015,
- A DPM exposure control value of 200 μg/m³ (TC) up to January 2017 and
- A DPM exposure control value of 160 μg/m³ (TC) in January 2018.
The 160 μg/m³ (TC) level is however subjected to review should new knowledge on the risks associated with excessive exposure to DPM become available.

They are used in lean mixture diesel engines. (Oxidation) converters burn HC and CO molecules with the assistance of a precious-metals wash coat. This process “converts” these harmful gasses into water vapor and carbon dioxide (CO2). It’s important to understand that converters are most effective when used with engines that have a lean air/fuel mix because this condition provides ample oxygen to “burn” the pollutants.
Catalytic converters have reductions off:
– Carbon monoxide (CO) from 85-98% – Hydrocarbons (HC) from 80-95% – Particulate Matter from 20-50%.
an exhaust emission control device that converts toxic gases and pollutants in exhaust gas from an internal combustion engine into less-toxic pollutants by catalyzing.
We offer a range of Catalytic Converters, which are fitted to the customers needs. For example : in Silencers, Incase it with cones, we cab add falnges as well as Pipe ends, This makes for easy fitting, Bolt on/Off or Camp on/Off.
- The PTX Diesel Purifier eliminates over 85% of carbon monoxide (CO), and hydrocarbons (HC).
- A PTX Purifier offers all the advantages, of a fast start-up, effective emission control and low backpressure. On average 3-9 in water gauge.
- Removes the smell of Diesel.
- PTX Purifier reduces the particular emission up to 85%.
- The product is generated by the process in the Diesel exhaust (carbon dioxide and water vapor) and are non-toxic to humans.
- High conversion efficiency
- Excellent mechanical durability , the design is resistant to vibration and axel forces
- A Very low pressure drop (only to about 1 kPa)

In a theoretically perfect combustion, carbon dioxide, water and nitrogen are the end products.
In reality, the incomplete combustion of diesel fuel results in emissions that include oxides of nitrogen (NOx), carbon monoxide (CO), carbon dioxide (CO2), water (H2O) and unburned hydrocarbons (HC). There are also unburned carbon particles, as well as engine oils, soot and ash particulates, which are known as particulate matter (PM).
The diesel particulate matter (DPM) id the visible cloud of black smoke that appears from engine start-up and continues to appear when engine is running.
- Diesel Emission gasses:
- HC – Hydro Carbon - unburnt fuel particle
- CO – Carbon Monoxide – Partially burnt fuel particle
- CO₂ - Carbon Dioxide – a green gas (GHG) by-product of the combustion process
- NO – Nitrous Oxide – a harmful gas
- NO₂ - Nitrogen Dioxide – a harmful gas
- O₂ - Oxygen
- D.P.M – a harmful gas
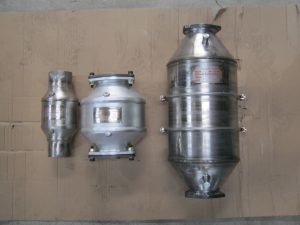
Passive regeneration accurse between 550°C and 600°C degrees. The engine needs to run at these temperatures for a minimum of 60% of engine working time to ensure regeneration, If this regeneration does not occur, there is a build-up of soot which will lead to the backpressure in the exhaust system to rise.
If this situation occurs the DPF filter will need to be removed from the machine and baked at 800°C for 8 hours, all depending on the level of clogging that has accrued. Air is then used to pulse through the filter to remove the remaining ash.
The baking of the DPF filter need to be conducted by Rush Exhaust & Rush Enterprises for the interim, on an exchange base, to reduce costs. Were a retrofit unit can be used.
For every 10 DPF filter in used a recommended 3 Units should be on standby to eliminate any down time, in the production line
- Position the catalytic converter followed by the DPF filter in the existing exhaust system as close to the engine as possible or where suitable space is available.
Installation
Maintenance
- Backpressure measurements must be taken on every major service or every 1000 operating hours.
- The diesel particulate filter must be cleaned every 1000 to 2000 hours, depending on what sulfur fuel is used. The higher the sulfur content of the diesel fuel the more maintenance will require.
Maintenance on the DPF consists of the following:
- If the back pressure reaches between 700 to 750mm of water gauge, the filter must be removed stripped and washed form outlet to inlet either with clean water or a degreasing fluid until no more visible soot is seen leaving the filter. Re-install and retake the back pressure readings.
- If the back pressure reading has not reduced back to between 200 to 300mm of water gauge a service exchange unit must be fitted and the filter must be send back to Rush Exhaust Purification for baking and further cleaning.
Baking of the filter consists of the following:
- The filter is burned at 800°C for 8 Hours and then re-flushed to remove ash and debris.
- This process might need to be repeated more than once, to make sure all contaminants and foreign debris in the filter is removed.
The Lifespan of a Diesel Particulate filter (DPF) and Catalytic Converter is between 8000 and 12000 operating hours, after which it needs to be replaced.
Worldwide emission standards are becoming stricter and require improved Catalyst s and Diesel Particulate filters specific to the market and individual application.
Rush Exhaust & Rush Enterprises provide Catalyst for power generation equipment and stationary applications complying with all current requirements and future limits.
Rush Exhaust & Rush Enterprises develop newest wash coat formulations and innovative catalyst coatings for applications all over the world. With profound knowledge in design and technical expertise, cooperation with OEs and accredited test labs our R&D achieves outstanding performance of the catalysts.
We work closely with our customers in order to meet all their requirements and to satisfy their demands. We continuously target on reduction of catalyst volume and precious metals.
Tailor made Catalyst and Diesel Particulate Filter solutions and completive precious metal amounts combined with our special coatings result in low light-off temperature, high durability and performance of our Catalyst and Diesel Particulate Filters.
Our advanced manufacturing equipment allows coating of standard honeycombs (metallic, wire mesh and cordierite/SiC) as well as substrates with structured designs.
Rush Exhaust & Rush Enterprise’s patented IMS design proved significant reduction of PM and all other emissions in many applications. The total PM reduction reached up to 63% in South African and American mining applications with continuous passive regeneration.
Catalytic Converter and Diesel Particulate Filter
New IMS System
Catalytic converter and Diesel Particulate Filter supplier Rush Exhaust and Rush Enterprises introduce a new metal block called IMS. The difference between the new catalytic blocks IMS and the structures currently used in exhaust emission filtration is in fact that emissions are mixed within IMS block and do not flow in between well-defined channels. Exhaust particles move between different layers of the spiral frequently getting in contact with surface active molecules. IMS can be used with gasoline or diesel vehicles
Revised Updated Offer IMS Filter:
As requirements to meet emission reduction going up we offer slightly redesigned IMS filter system.
1. We will modify filters inside structure, by reducing the openings to some point where gases will have more time to interact with catalytic surface. Gases will be spread on 100% of the active area and with added turbulence will reduce all „bad” elements.
2. We will add PGM to current loading and in addition we will add Rhodium as active ingredient to reduce NOx.
3. We will also use more advance wash coat material which will help PGM to be more active which will significantly improve performance of the system.
With all above mentioned changes we can confirm that in general performance of the System will increase by 50-60%. PM will be reduced by 70-80%, NOx by 60% and other gases like CO, HC, and THC will achieve reduction by 80-90%.